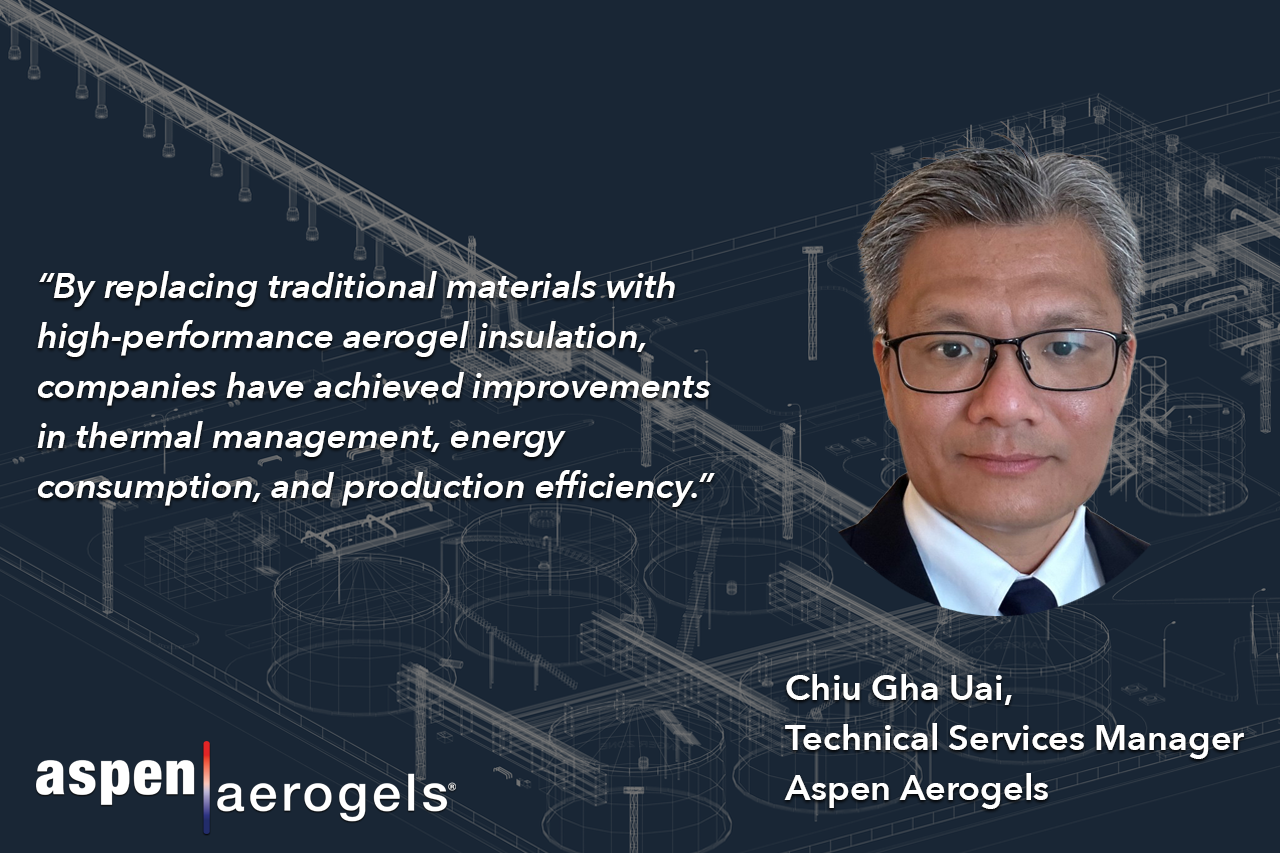
The global refining industry is at a turning point. With tightening margins, volatile feedstock costs, rising operational expenditures, and fluctuating demand patterns, refiners are under pressure to unlock new sources of profitability. In this evolving landscape, many operators are reevaluating long-standing assumptions around cost management and operational efficiency.
One often-overlooked lever that’s now gaining attention is industrial insulation—specifically, advanced insulation materials such as aerogels. Long valued for their thermal performance in niche applications, these next-generation materials are proving to be a critical, scalable solution for refineries and petrochemical facilities worldwide seeking to reduce costs, improve reliability, and advance sustainability goals.
This article explores the same themes that will be covered in our upcoming presentation at Asian Downstream Summit, where we’ll dive deeper into real-world case studies showing the measurable impact of insulation innovation on refinery and petrochemical operations.
Rethinking Energy Efficiency in Thermal Systems
Thermal efficiency is a foundational metric for any refinery, and the role of insulation in achieving it cannot be overstated. Traditional materials—while cost-effective at the outset—often degrade under mechanical stress, absorb moisture, and lose performance over time. By contrast, Aerogel insulation, offers a step change in performance. Its ultra-low thermal conductivity helps retain process heat more effectively, even in harsh or compressed conditions.
These advantages contribute to reduced heat loss during manufacturing processes and more consistent temperature control across heat-sensitive operations. In practice, this has led to faster production times, better thermal management, and more efficient production cycles, especially in case studies from facilities that have transitioned away from legacy insulation.
By minimising energy waste, aerogel-based systems also cut fuel consumption—critical for operators facing both high energy costs and carbon constraints. This results in lower operational expenses and increased yield, improving both economic and environmental performance.
Strengthening Asset Integrity and Uptime
Corrosion under insulation (CUI) remains one of the most costly and persistent risks to thermal infrastructure. Traditional insulation materials can trap moisture and allow it to migrate across surfaces, creating hotspots for corrosion. In contrast, aerogels are hydrophobic and breathable, allowing trapped moisture to escape without compromising thermal integrity.
By mitigating CUI and maintaining long-term performance, these materials have been shown in field studies to extend asset life, reduce unplanned shutdowns, and minimise long-term maintenance costs. This translates into tangible cost savings and improved asset availability for industrial operations.
Installation Efficiency and Lifecycle Value
Ease of installation is another benefit that case studies consistently emphasise. Aerogel blankets are lightweight, flexible, and easy to install in tight or congested spaces, including around bends, valves, and elevated lines. This leads to shorter installation times and improved worker safety—especially during retrofits or urgent maintenance projects.
Furthermore, aerogel systems can often be removed, inspected, and reused without significant degradation. This reusability lowers total lifecycle cost and supports efficient maintenance practices.
Supporting Process Control and Throughput
Consistent thermal performance is crucial for process control, particularly in continuous operations such as catalytic reforming, amine treatment, or crude distillation. Advanced insulation helps prevent temperature fluctuations that can cause product variability, slowdowns, or fouling.
In the real-world applications we’ll share during our presentation, companies using aerogel insulation experienced enhanced process stability, leading to higher product quality, reduced downtime, and greater overall throughput.
Driving Sustainability and Global Competitiveness
Today, insulation decisions are not just about safety and thermal loss—they’re also about energy policy compliance and market positioning. Advanced materials like aerogels help operators meet global sustainability goals by reducing Scope 1 and Scope 2 emissions, improving energy efficiency, and aligning with ESG reporting frameworks.
In addition to the environmental benefits, this transition has strengthened the competitive positioning of adopters by improving energy KPIs, reducing carbon taxes, and qualifying for government incentives or carbon credits in certain jurisdictions.
Case studies from the petrochemical and refining industries show that adopting high-performance insulation can yield long-term energy savings, reduced emissions, and a more resilient operation overall.
Conclusion
As Chiu Gha Uai, Technical Services Manager at Aspen Aerogels, will discuss in greater detail at Asian Downstream Summit, the shift to advanced insulation materials is not just an upgrade—it is a strategic imperative. Across the globe, refiners and industrial operators are using aerogels to achieve measurable gains in energy efficiency, process control, production yield, and environmental impact.
Whether your goal is to reduce energy losses, meet emissions targets, or future-proof your facility against rising energy costs, advanced insulation can deliver a proven, scalable solution. Join us to explore how material science is shaping the future of operational efficiency and sustainability in the industrial sector.
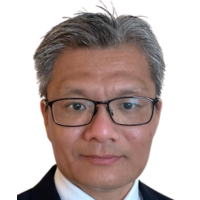
Chiu Gha Uai
Technical Services (Asia) Manager, Aspen Aerogels Inc., Malaysia
Mr. Chiu has more than 15 years of engineering management experience, of which, 8 years of field application, installation, design and consultation in heavy industries, and more recently, over 7 years in energy and hydrocarbon processing, involved in engineering design, installation, and consultation. He is currently based in Malaysia as the Asia Technical Services Manager in Aspen Aerogels.